Reduction of nitrous oxide emissions and precious metal consumption in the industrial oxidation of ammonia through AI-based development of new catalysts
Catalysts are used in around 80% of all chemical processes. However, there is a lack of general understanding of which catalyst is ideal for a particular chemical reaction. Existing catalysts are usually the result of accidental discoveries. The classic Ostwald process for the production of nitric acid is a highly relevant industrial example. Nitric acid is one of the most widely produced bulk chemicals in the world, with an annual production of more than 60 million tonnes. In the first step, known as ammonia oxidation, catalysts made of platinum-rhodium all
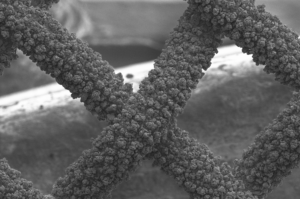
oys are used and nitrous oxide is produced as an undesirable by-product. Nitrous oxide is a greenhouse gas 300 times more potent than carbon dioxide. The high global production volume of nitric acid leads to nitrous oxide emissions of around 100 million tonnes of CO2 equivalents per year. A second problem is changes in the catalyst. During operation, the structure and composition of the catalysts changes, which leads to a considerable loss of platinum from the catalyst. Despite these two clear limitations, no improved catalyst has yet been found.
With virtual high-throughput screening approaches based on artificial intelligence (AI), these limitations can be overcome. This approach enables an enormous number of material compositions to be tested virtually. However, the theoretical methods are still quite new and there is no corresponding software for routine use. As a result, this approach has not yet found its way into industrial practice.
This is where the joint project ReLaKIKat comes in. It is developing such an AI-supported screening and demonstrating how the method leads to a new catalyst. For the first time, the strategies will also consistently take catalyst stability into account. The entire workflow for catalyst optimisation will be demonstrated using ammonia oxidation. The newly introduced catalyst will make a long-term contribution to achieving climate targets. The new AI-based method for finding new and improved catalysts for chemical processes also represents a breakthrough in catalyst research for the development of new green technologies.