Materials for Industrial CO2 utilisation: from Electrocatalyser to Sustainable Electrode
As an energy-intensive industry and due to the high share of products of fossil origin, the chemical industry is currently responsible for around 15 % of German greenhouse gas emissions (Scope 1-3). Important steps on the path towards climate neutrality by 2045 is therefore the substitution of fossil raw material sources and the integration of electricity from renewable sources into the production processes. By capturing CO2 from unavoidable exhaust gas streams from various industrial processes (e.g. cement or steel production), biorefineries and, in the long term, via direct air capture, an alternative source of raw materials is available that can take on the role of a C1 building block to produce a variety of basic and fine chemicals.
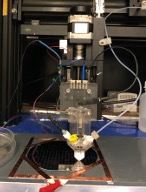
The electrochemical production of CO2 at the cathode of an electrolysis cell enables the production of currently largely petrochemical platform chemicals such as carbon monoxide (CO), ethylene, ethanol or propanol from CO2, water and renewable electricity. The production of CO is the most advanced in terms of technology maturity, which is why this reaction is also considered an entry-level technology for the commercialization of CO2 electrolysis. Based on this, the production of additional products can be established on a large scale in the medium and long term through further developments at the catalyst and the electrode level.
This aspect is to be taken up within the scope of the present project and considered through two parallel development strands with a focus on electrode and catalyst development. Production of CO is particularly attractive as a starting point because it is a high-cost platform chemical that is used as a starting point for numerous chemical syntheses.
The currently achievable key figures for electrolysis are far from sufficient for the commercial realization of the process. In this context, the porous gas diffusion electrode (GDE), in which the catalyst is integrated and in whose interior the reaction zone is formed, is one of the most important elements of the electrolysis cell, as together with the catalyst it determines the space-time yield (achievable current densities). The specific energy input (overvoltages and selectivity) and the long-term stability are determined.
At the same time there is a significant need for action on the supply of raw materials and in terms of sustainability of the used raw materials. The commonly used material for the electrode binder is PTFE, one of the per- and polyfluorinated chemicals (PFAS) materials from the published ECHA restriction dossier and, according to the current status of the dossier, must be substituted for the use in electrolysis systems. Currently no alternative binder is available with which a similar performance can be achieved. The precious metal silver is used as catalyst and is necessary for important future technologies such as photovoltaics (current demand is around 2000 t/year) and other technologies such as radio tags (RFID). For 2030, it is estimated that demand from these new applications could be as high as 83 % of the 2006 annual production of 19,000 tons. The range of silver reserves is estimated to be only 20 years away.[1] To address this uncertainty, the development of an alternative GDE composition must be investigated in a timely manner in view of the planned commercialization of CO2 electrolysis.
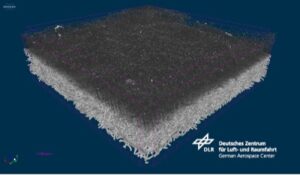
With the project DisCO2very, besides the development of novel, precious-metal-free catalysts, an extensive screening of alternative fluorine-free binder systems and their integration into GDEs will be carried out in order to substitute silver and PTFE without loss of electrode performance. With regard to the catalyst, the suitability of multi-metal catalysts will be studied, which belong to the new material class of high-entropy alloys. In addition, promising M-N-C catalysts (with M = transition metal) will be developed and tested for electrochemical CO2 reduction (CO2RR), as single (SAC) and as dual-atom (DAC) variants. Both, the DAC and the multi-metal catalysts are largely unexplored with regard to CO2RR but have very high potential due to their range of active centers with different adsorption energies and the huge range of optimization options.
In order to be able to test a variety of catalyst systems, an AI- based high-throughput procedure is used for benchmarking in specially developed measurement setups. At the same time, recyclability is assessed, and further developed, while economic viability is analyzed and a comprehensive sustainability assessment conducted.
Further information
“Ressourceneffizienz und ressourcenpolitische Aspekte des Systems Elektromobilität“ (OPTUM Projekt), Studie des Öko-Institut