Methane degradation in industrial exhaust air through innovative combination of gas scrubbers with photocatalytic reactors
Methane is the most common and at the same time the simplest hydrocarbon in the atmosphere. Due to its uniquely high hydrogen-to-carbon ratio, methane is highly relevant as a fuel. However, it acts as a potent greenhouse gas in the Earth’s atmosphere due to its absorption behaviour of electromagnetic radiation in the infrared range. In view of the climate crisis, it is essential to reduce emissions of greenhouse gases such as methane into the atmosphere. Otherwise, the warming of permafrost soils within the Arctic and boreal ecozones, among other things, will cause additional large quantities of methane to enter the Earth’s atmosphere in an uncontrolled manner. While several strategies for reducing methane emissions have been identified and implemented for the energy and industrial sectors or the waste sector, the recommendations for technical solutions in the agricultural sector of animal production that have so far been considered practicable are very limited. However, in the case of animal husbandry in closed stables, there are potential points of application for methane reduction due to the exhaust air systems that are necessary anyway. However, there is currently no usable technology on the market for the reduction of low methane concentrations from complex industrial matrices. For this reason, the current version of the TA-Luft (“Technical Instructions on Air Quality Control”) does not legally prescribe the reduction of methane but merely recommends it.
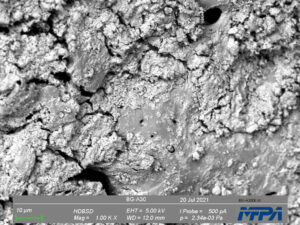
© MFPA Weimar
With their project, the joint partners are targeting precisely this technological gap. Through the innovative combination of newly designed gas scrubbers for fixing inorganic pollutant gases, polar organic substances, dusts and bioaerosols and photocatalysts modified for this special application, it will be possible to significantly surpass the state of the art. A special focus must be placed on the development of modified photocatalyst reactors. On the one hand, these will act on the water phase of the gas scrubbers in order to mineralize the dissolved organic substances and reduce the biological load, so that an alternative use of the water phase as a fertilizer can be developed. Instead, the gas phase is fed into photocatalytic reactors to completely eliminate unpleasant odours and mineralize VOCs that cannot be washed out. In the course of this, the photocatalytic materials used are to be modified in such a way that they have a significantly higher selectivity for non-polar organic compounds. Very volatile organic compounds (VVOCs) such as methane in particular have an increased global warming potential. For this reason, this development step represents an innovation with great leverage, as exhaust gas flows with low VVOC concentrations also occur in other industrial areas (e.g. waste sorting).
There is a need for special flue gas cleaning technology because reductive adsorption filters (e.g. granulated activated carbon) are not able to adsorb this group of VVOCs. At higher methane concentrations, flares or oxidation windows are installed for this reason, which burn these gases. However, as the concentration of combustible components in the flue gas is not sufficient to ensure that the flare burns independently, fossil fuels would have to be added, which in turn leads to a significant additional carbon footprint. In addition, wherever activated carbon filters are used to adsorb all other organic pollutant gases, regular replacement of the loaded filter media is necessary. Here too, considerable quantities of greenhouse gases are emitted during the transportation and thermal utilization of these loaded filter media. The adsorption filter-free technology of photocatalytic oxidation allows UV radiation to be used, which can be made available in a very energy-efficient manner thanks to the ever more powerful LED technology.
To implement the combination technology of modified gas scrubbing and selectivity-enhanced photocatalysts, MeGaPho is working on two different tasks:
In the first task, the two-stage process for the innovative combination of gas scrubbers and photocatalytic reactors for the purification of complex matrices in biogenic and industrial environments is being developed. During the development of the scrubbing modules, both continuous and alternating batch operation at different pH values are to be investigated in order to increase the solubility or possibilities for chemical fixation of the compounds to be washed out. In addition, the process requires a suitable filtration or sedimentation unit. Among other things, packed columns are used as a starting point for transferring the pollutants from the gas phase to the water phase. The scrubbing modules developed in this way are also equipped with photocatalytic reactors, which are designed to significantly reduce the organic load of the scrubbing water. The technical target parameters specified by the TA-Luft (at least 70% NH3, dust and bioaerosol reduction) are to be achieved and exceeded at this point.
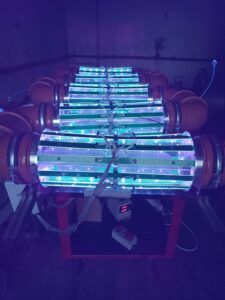
The artificially illuminated photocatalytic reactors for cleaning the gas phase must contain a suitable foldable support structure with an innovative geometry to increase the reactive surface area. Extensive fluid dynamic modeling will contribute to this. The installation of a drying stage must be examined in order to reduce the water load. This will significantly increase the effectiveness of an additional ozonation unit as a “booster” for photocatalysis. In addition, materials for concentrating the VVOCs out of the gas stream are being investigated in order to increase the degradation efficiency at the catalyst and enable alternative utilization of the concentrated methane gas matrix.
In the second task, novel Titanium dioxide (TiO2) photocatalysts are being developed for the water and gas phase. For the new development of photocatalytic surfaces for use in the water phase, these are applied to a carrier framework (stainless steel, carbon fiber), which is electrically conductive. The project will develop a suitable electrode material and characterize the electrochemical parameters so that electrolysis is excluded. This poses a particular challenge due to the varying properties (ionic strength, pH value) of the aqueous solution. The usefulness of this reactor modification is that the anodic switching of the photocatalyst in the aqueous phase can suppress calcification on the one hand and recombination of the electron-hole pairs on the other.
In addition, different methods for modifying the photocatalytic particles and surfaces are developed and compared both before and after coating. The coatability of the modified particles must then be investigated and the geometry and surface properties of the carrier materials adapted (e.g. using primers). The aim is to partially hydrophobize the superhydrophilic TiO2 surface in the excited state so that the residence time of hydrophobic gas molecules (VVOC) on the catalyst is increased. In this way, even small non-polar molecules within the real matrix should be photocatalytically oxidizable.
In this way, the project aims to reduce greenhouse gas emissions in two ways, as it is intended to prevent potent greenhouse gases such as methane from entering the atmosphere and at the same time minimize the use of adsorption filters and the associated CO2 emissions if used appropriately. The project deliberately focuses on processes with low methane concentrations in complex exhaust gas matrices in order to close the existing technological gap. During the development of the process, the focus is on captured material flows.