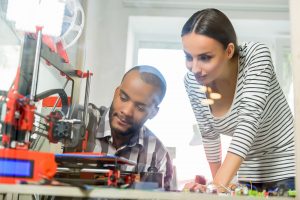
3D printing has boomed in recent years, even for private use, as 3D printers and printed materials are available at low cost. 3D printing here refers primarily to the low-cost FFF process. In this process, a three-dimensional part is created from a plastic that is available in a suitable form, e.g. as a wire on a coil, by means of a molding process. It is not always necessary to “shoot” a material through a printing nozzle for this purpose; there are many other processes, e.g. selective laser sintering, in which powders such as the polyamide (PA) described below are fused by laser. However, laser sintering is much more expensive than the FFF process.
There is a very large variety of materials that can be 3D printed; in addition to the classic thermoplastic polymers, these also include metals and ceramics, as well as plastics containing ceramics, carbon fibers, glass fibers or wood, and reactive (i.e. polymerizing during printing) plastics, including silicone-based materials [1]. Inorganic materials such as concrete for house construction and paper in lamination technology as well as waxes are also among the 3D printing materials. Completing the wide range of 3D printing materials are specialty materials such as pharmaceuticals, living cells, and the growing field of foodstuffs such as chocolate, baking dough, butter, cookie dough, hazelnut cream, marzipan, cream cheese, fruit gum, gelatin, pasta dough, mashed potatoes, chewing gum, or sugar.
In addition, there are a variety of mostly highly focused research applications of 3D printing with other materials that are not accessible to citizens and are not the focus of this article.
Instead, this article describes only some of the widely used plastic (polymer) 3D printing materials. It is not possible to comprehensively cover the topic and the materials used, also due to the constantly growing number of available materials.
Common 3D printing materials and their processing
PLA – Polylactid acid
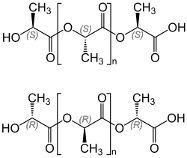
Polylactic acid – PLA – (according to the IUPAC standard called poly(2-hydroxypropanoic acid)) is a plastic that can be produced from corn starch via the intermediate stage lactic acid (2-hydroxipropanoic acid). It is also possible to produce PLA from petroleum. Because of its natural base material, corn starch, PLA is considered a “biological” plastic. It is theoretically biodegradable, but because of its polymeric form, this happens very slowly under normal conditions [2]. PLA does not release any harmful substances at room temperature and is therefore compatible with foodstuffs. Nevertheless, dust formation should be avoided during use and vapors/mist/gas should not be inhaled, because harmful substances can be formed during heating [3]. No special environmental protection measures are required. Likewise, pigments or other additives may be present, which should also be considered critically. Thanks to a relatively low melting point (150-160°C, printing temperatures are well above the melting point for all materials), PLA can be easily printed using heated nozzles. In addition, PLA is commercially available at a relatively low cost (approx. 20 € per 1kg coil).
ABS – Acrylonitrile butadiene styrene (copolymer)
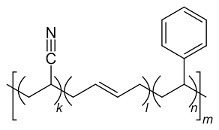
ABS is another plastic used for 3D printing. It is made from petroleum. ABS is widely used; Lego bricks and Playmobil figures are made of it. However, these toys are not 3D printed. ABS is also readily available and inexpensive. The basic building blocks styrene, acrylonitrile and butadiene, from which ABS is built, are organic chemicals with some hazard potential. During the 3D printing process, even under normal processing conditions, traces of the basic building blocks, decomposition products and additives can evaporate. For printing with molten ABS, this effect is amplified and good ventilation of the room is strongly recommended. ABS melts at 210 – 250°C.
PA – Polyamide (Nylon)
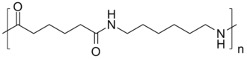
Polyamides (PA) are commonly referred to as nylon in the 3D printing environment, which is only correct to a limited extent. There are various polyamides that are very similar, but not identical. Nylon is the brand name of an American manufacturer that refers to only one PA variant (polyamide brand names that describe other polyamide variants are Perlon, Dederon, etc.). PA is also in the end made from petroleum, the plastic uses construction principles as they occur in natural proteins. Nevertheless, PA is not biodegradable. PA is also commercially available and can be considered non-hazardous. However, irritant vapors can form during processing or under normal operating conditions. Therefore, adequate ventilation must be provided. It is not expected that fibers will be released under normal conditions of use.
PET – Polyethylene terephthalate (and variants such as PETG)
PET is known through beverage bottles. It belongs to the polyester family and is relatively stable, flexible and transparent in thin layers. Contrary to repeated rumors, PET plastics do not release any hormone-like substances, according to information from the German Federal Institute for Risk Assessment BFR. Likewise, the BFR gives the all-clear regarding the release of antimony(III) oxide, which is used in the production of PET and is incorporated in parts into the manufactured plastic: it can only be detected in PET bottled mineral water in concentrations far below the permitted limits.
PETG is a variant of PET and indicates a plastic in which PET has been modified in the glycol component; it melts at 220-240°C. Elements printed from PETG can even be sterilized and are therefore also used in medical technology. In addition to its high resistance and optimum mechanical properties, PETG is resistant to chemicals, flame retardant and certified as a food-safe polymer. Therefore, it is used for processing as well as for packaging food, but also in the pharmaceutical sector. In addition, this material is 100% recyclable. PETG is said to combine the advantages of ABS (temperature resistance, durability and strength) and PLA (easy to use) in one filament.
Safety aspects in 3D printing
A material safety-relevant release of substances (e.g. ultrafine particles or volatile substances) can occur both during preparation and post-processing, as well as during 3D printing itself. A distinction must be made between mechanical abrasion during pre- and post-processing as well as a thermal release during preparation and the actual printing[1].
The materials described here are printed by melting, which usually means that a material is present as a plastic wire that is pressed through a heated nozzle (similar to a hot glue gun) and then produces a highly viscous material stream that can be modeled in three dimensions. Depending on the melting point of the material used, it must be brought to a temperature just above the melting temperature for this purpose.
On the one hand, when the material melts, the starting chemicals used in the production of the material can be released, especially if the polymerization process has not been completed (which is possible in production). Added additives and pigments can also be released. On the other hand, heating the material during the printing process can produce and release decomposition products, especially if the melting point of the material is by far exceeded.
In both variants, hazardous substances can be released. It is therefore generally advisable to keep the printing chamber closed during 3D printing, if possible, and to ventilate the working room well during and after printing. Ventilation during printing, however, can lead to poorly formed and mechanically less stable print products.
Mechanical abrasion, e.g. when grinding the completed print object, mainly releases small particles called fine dust and ultrafine particles. Volatile organic compounds (VOCs), which are contained in the plastic, as well as colorants and pigments, may also be produced during sanding.
Conclusion
3D printing is not only a technical application, but also a versatile activity for creative hobbyists. Health aspects should not be neglected in any case. For this purpose, good ventilation of the workplace should be ensured and, if necessary, a respiratory protection mask (FFP2 or better) should be worn.
Literature:
- Bourell, D et al. (2017), CIRP Annals, 66, Issue 2, 659-681
- Tokiwa, Y et al. (2006), Applied microbiology and biotechnology, 72(2):244-251.
- Wojtyła, S et al. (2017), Journal of Occupational and Environmental Hygiene, 14(6), D80-D85